The long road from needle coke to graphite electrode
The production of graphite electrodes is highly complex in terms of manufacturing technology and takes several weeks. Needle coke and coal tar pitch are used as raw materials. The production process for manufacturing graphite electrodes is divided into the following steps: Forming, baking, impregnation, re-baking, graphitisation and machining.
Step 1: Forming
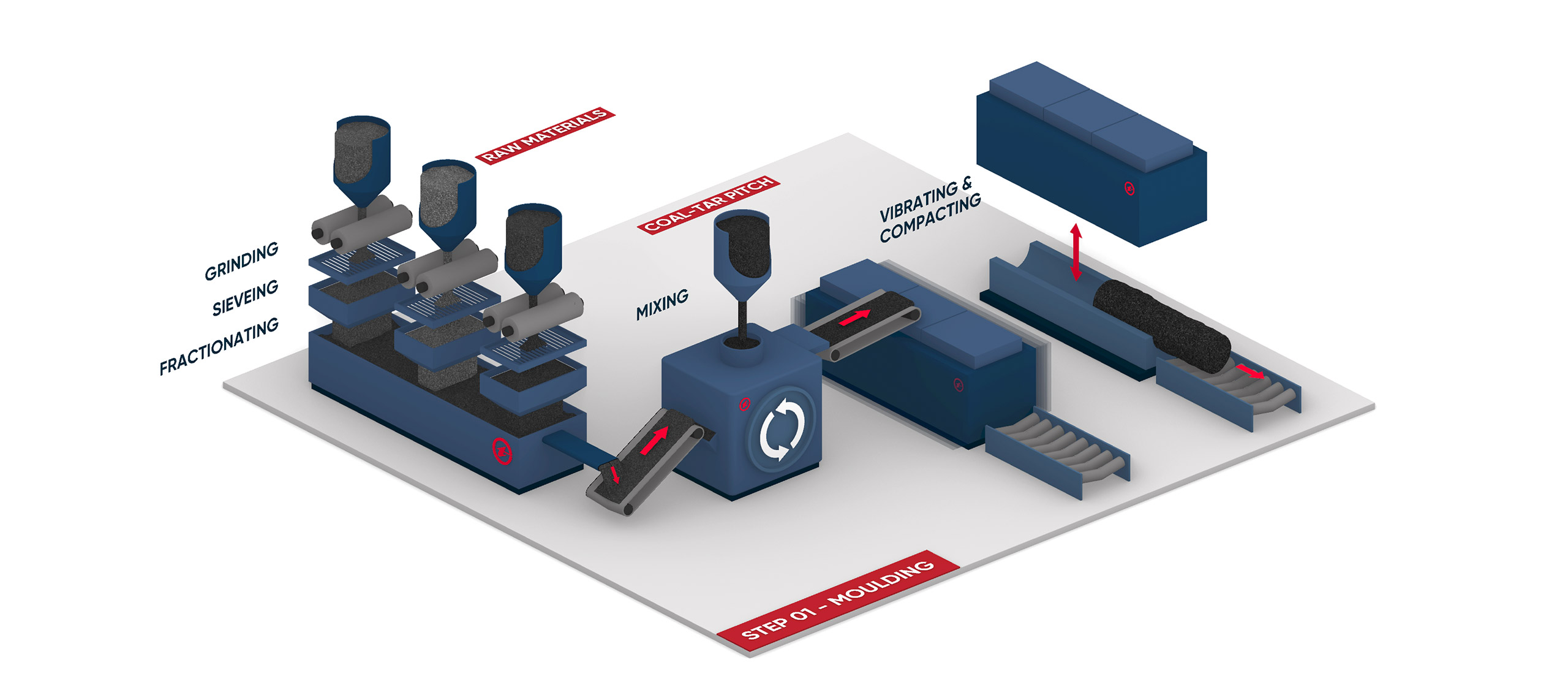
One of the most important process steps is forming. TOKAI ERFTCARBON uses the vacuum vibration method for this. For this purpose, the needle coke is first grounded, sifted, fractionated and then mixed, taking into account product-specific recipes. The coke mixture is fed via an encapsulated transport system equipped with filters to a compact mixing system, also encapsulated, where it is mixed together with liquid hot coal tar pitch to form the so-called “green mass”. This is then poured into a mould box, which is sealed and evacuated. The mould is then shaken on a vibrator and the mass is brought into the cylindrical electrode mould under high pressure.
Step 2: Baking
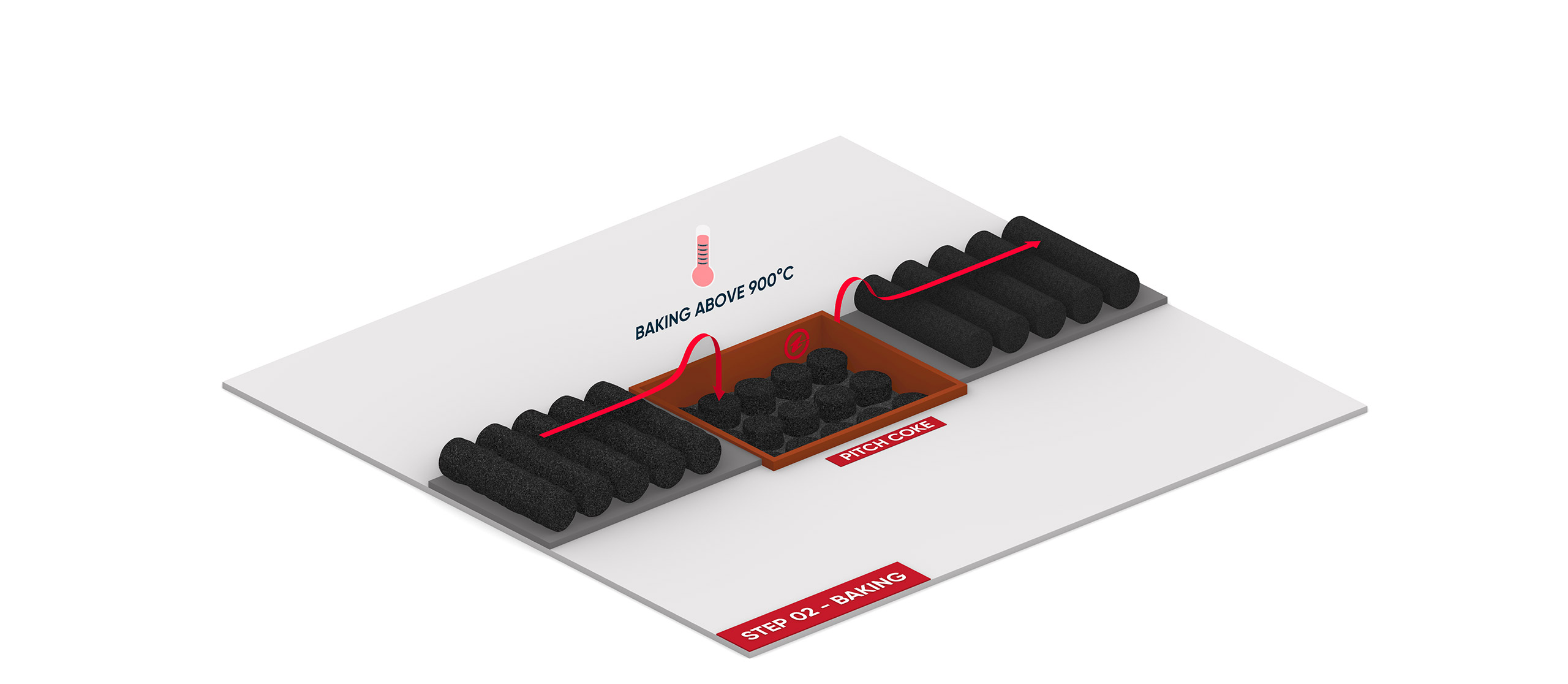
In a ring furnace fired with natural gas, the electrodes are baked at temperatures above 900°C for a period of 1 month. The combustion chamber into which the moulded parts are placed is filled with mine coke. On the one hand, this serves as protection against oxidation, and on the other hand, the material ensures that the temperature is transferred evenly to the moulded parts. After the baking process, the coke is completely sucked out of the combustion chambers, the electrodes are withdrawn from the chambers and the adhering filler material is removed. The coke is processed and is then available again for the next baking cycle.
Step 4: Re-baking
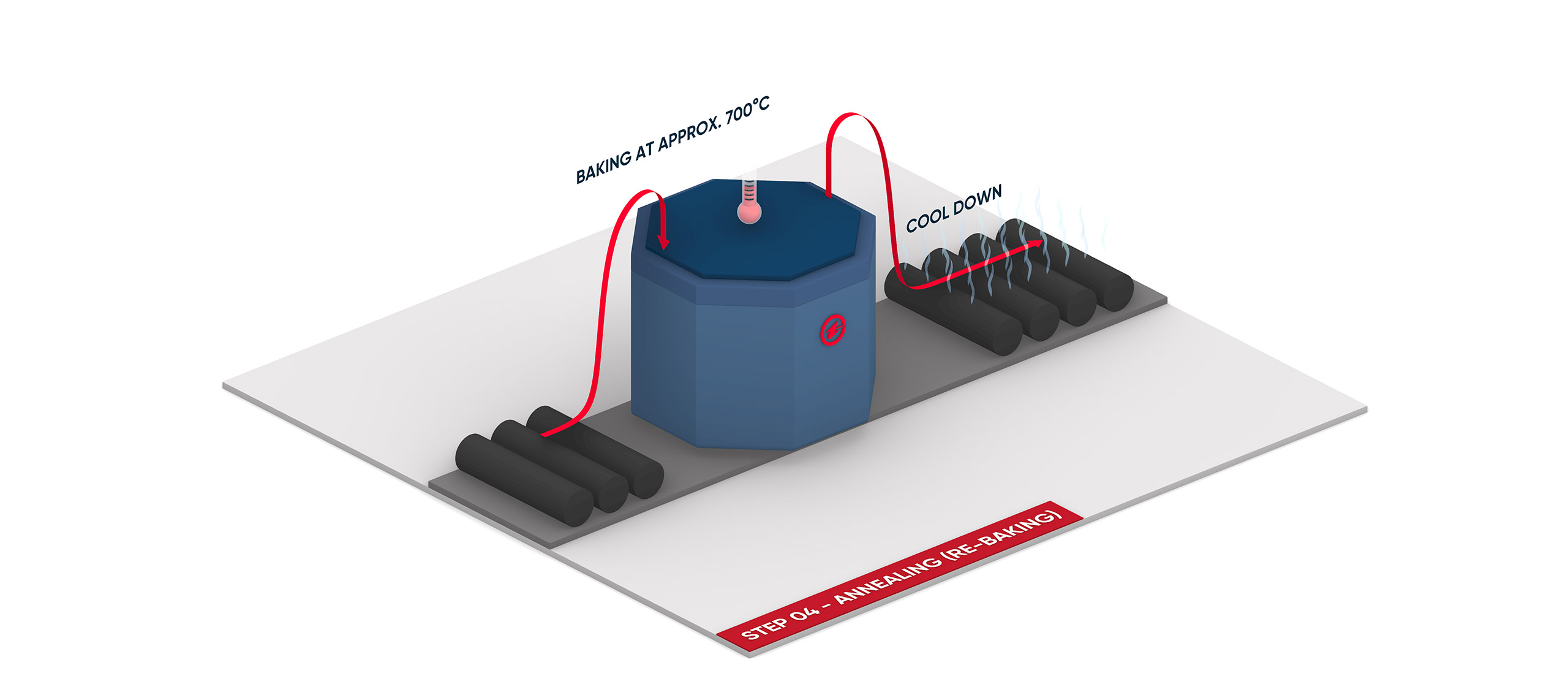
After removal from the autoclaves and subsequent cooling in a water bath, the electrodes are placed in re-baking furnaces fired with natural gas. In this further baking process, the tar pitch that has penetrated the bodies is converted into pitch coke at approx. 700 °C. This process takes several days. For operational reasons, the re-baking process can also take place in the ring furnace used in the baking operation described above, which adds four weeks to production time.
Step 5: Graphitisation (conversion into graphite)
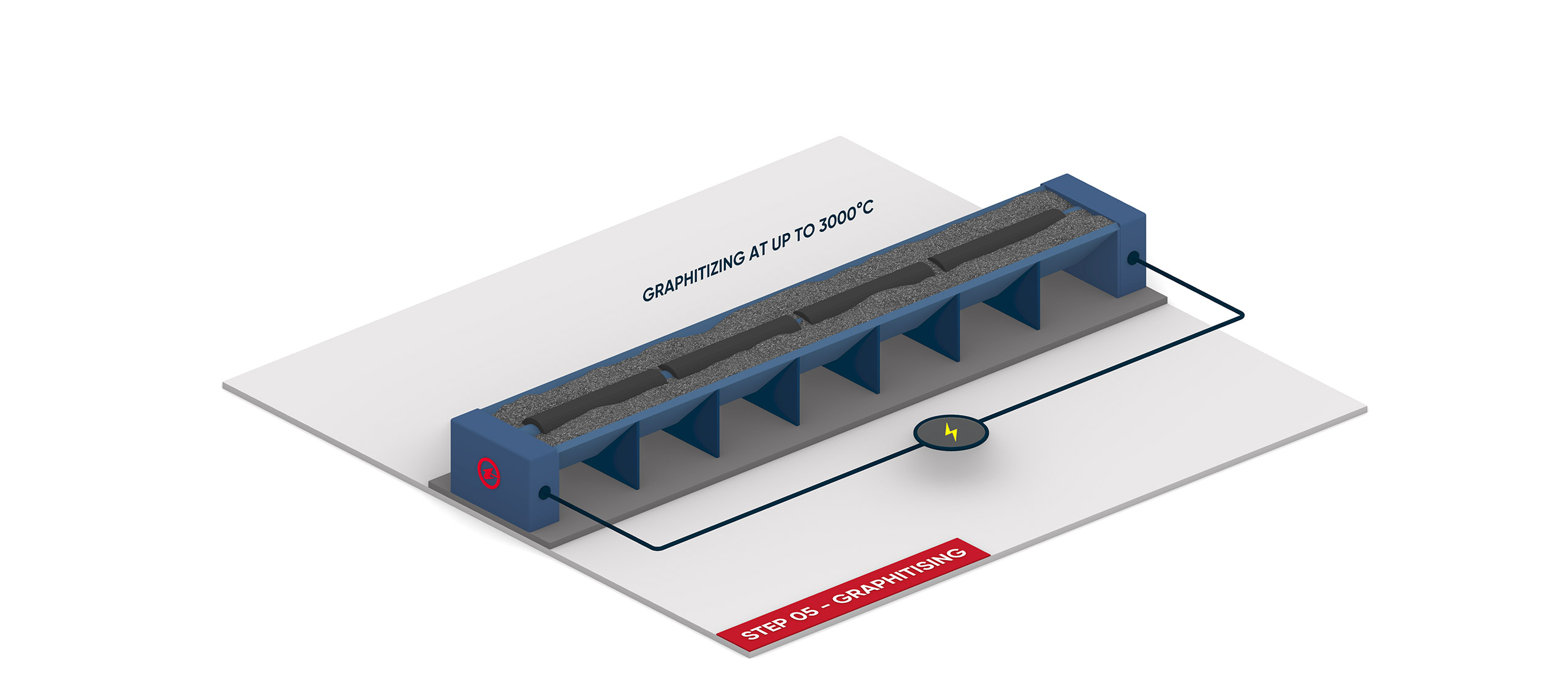
For graphitisation, the electrodes are joined together to form a strand, placed in a furnace and energised. The “resistance heating” heats the strand up to 3,000 °C. At these temperatures, amorphous carbon transforms into crystalline carbon (graphite). The process takes up to 15 hours. The subsequent cooling time is 1 week. The mine coke, which is also used here as a filling material, is then completely extracted, filtered and returned to the production process.
Step 6: Machining
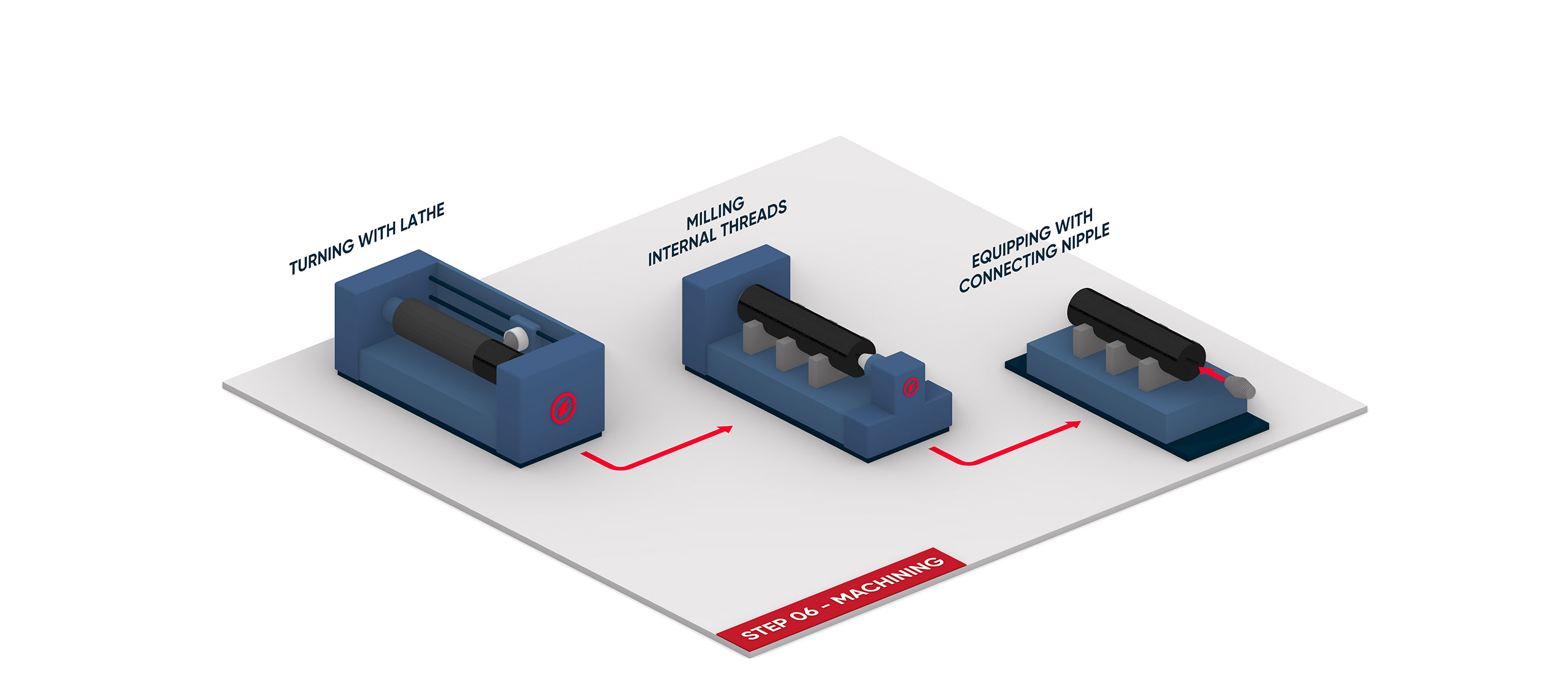
In the final production step, the graphite electrodes are given their final dimensions by machining. Internal threads are milled into both ends of the electrode and one end is fitted with a biconical threaded piece (nipple). This means that the electrodes can later be screwed together into a strand at the customer’s site.